Home> Company News> Replacement of hub bearing automation equipment
- Address253 Paya Lebar Road #12, Singapore 408023
- Factory Address253 Paya Lebar Road #12, Singapore 408023
- Worktime9.00-18.00
- Phone(Working Time)65-65201318
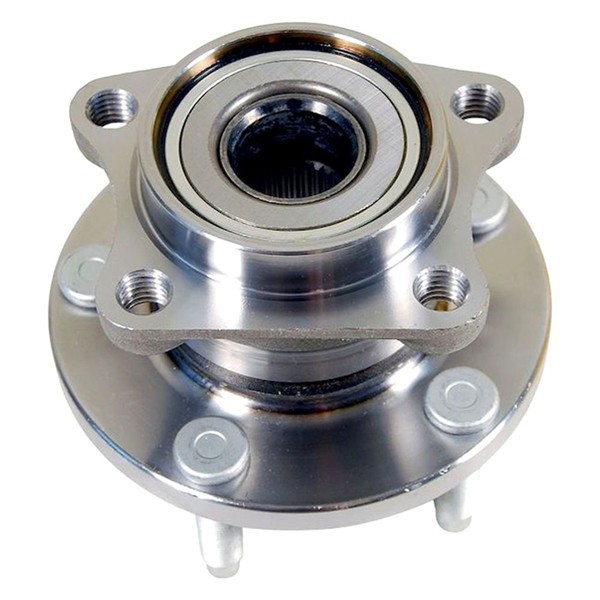
1. Development of wheel bearings
The automotive hub bearing unit is mainly subjected to the weight of the vehicle (radial load) transmitted through the suspension system, the axial load generated by the steering of the vehicle, and the torque transmitted from the transmission and the drive shaft. Wheel bearings can be divided into first, second, third and fourth generation wheel bearings according to different ways of integration with other components of the automotive transmission system. At present, the third-generation wheel bearing is widely used. It adopts the bearing unit and the anti-brake brake system ABS. The inner and outer rings of the bearing unit are flanged, and the inner ring is bolted to the drive shaft through the inner flange. The outer flange mounts the entire bearing together.
2. Manufacturing process
At present, the main processing processes of bearing manufacturers are divided into two types: the turning process of the first machining process is mainly concentrated before the heat treatment of the workpiece, as shown in Figure 1. The advantage is that the processing process before the high-frequency quenching can be uniformly processed by the automatic production line, the processing time is shortened, the processing efficiency is improved, and the cost is greatly reduced. The disadvantage is that the high-frequency quenching causes the dimensional positioning surface of the grinding raceway process, the bearing surface of the hub bearing unit and the brake disc and the steel ring to be slightly deformed, thereby affecting the accuracy of the channel grinding and the position of the bolt hole. Conducive to the stability of the bearing unit operation
Sex, reliability and service life. The turning process of the second processing process is mainly distributed in the roughing process before the heat treatment of the workpiece and the finishing process after the heat treatment. The utility model has the advantages of effectively eliminating the influence of the high frequency quenching on the three positioning surfaces mentioned above, ensuring the precision of the channel grinding, and improving the position of the bolt holes, thereby greatly improving the stability and reliability of the bearing unit and prolonging. Bearing unit life. The disadvantages are that there are many processing steps, the processing equipment is dispersed, and the investment cost is high.
3. The automatic processing before centralized processing of heat treatment is mostly roughing process. The equipment is composed of truss automatic line and truss manipulator and two CNC lathes (OP10 and OP20), loading and unloading warehouse, turning mechanism and sampling unit. The rough finishing process before the heat treatment can be completed. The truss is in the form of 1v2, ie a robot refuels two lathes. The robot refuels the main unit for 16 seconds. The drilling and tapping process of the hub bearing is completed by a workstation composed of loading and unloading robots. A joint robot is equipped with three vertical machining centers. The loading magazine has an angular positioning function, and the auxiliary robot feeds the vertical machining center. Three vertical machining centers process the same process, reducing the production line of automatic lines
beat. The robot refuels the main unit for 16 seconds.
4. After the heat treatment, the automation equipment of the finishing process is processed by the heat treatment of the hub bearing flange surface, because the cutting amount is small, the feed speed is fast, and the processing time of a single workpiece is short. General automation equipment can not meet the fast beat requirements of wheel bearings, most of the supporting manufacturers are still using manual single machine processing, a very small number of wheel bearing brand manufacturers
In the case of processing with imported equipment, in this case, our company has developed a special machine automatic production line for wheel bearing precision cars.
(1) Overall structure layout
At present, there are two kinds of mainstream automation equipments for lathes, one is the truss type robot automatic loading and unloading, and the other is the lathe external joint robot refueling form. Both of these forms are outside the machine, and there are switching gates and excess movement time during refueling, resulting in a refueling time of around 18s. The same processing time, low efficiency, resulting in unreasonable production line beats. The new finishing process automation equipment adopts the form of in-machine robot, and the 6-axis joint robot is hung inside the CNC lathe, which saves the switch door time when the machine tool is refueling, and greatly improves the refueling cycle. The independent frame design solves the vibration of the machine tool and ensures the stability of the machine tool. After the heat treatment of the hub bearing, it is transmitted to the automatic line of the finishing car through the conveying channel, and the workpiece is turned over by the turning mechanism to reach the loading state during the processing of the hub bearing, and then sent into the inside of the machine, and the robot manipulator grabs the bearing piece of the wheel hub and waits in the waiting area. , part plus
After the work, the robot reworks the workpiece to the main machine, replaces the finished hub bearing, and then rotates the sixth shaft of the robot to load the hub bearing blank into the main fixture. The machine enters the machining program. At the same time as the main machine cuts the workpiece, the robot exchanges new blanks inside the machine, waiting for the machine to complete the machining. The above process starts and the drum is kept at the production line for 22s.
(2) Processing fixture and dustproof treatment
The equipment is processed for dry cutting. The IP67 grade protection of the robot can effectively protect the dust generated during cutting and prolong the service life of the joint robot. The workpiece grips the raceway surface through a specific rear pull chuck.
Position the hub bearing against the surface to ensure machining accuracy. The center of the hub bearing is added to the center of the road to ensure the machining of the workpiece.
When the center hole position generates a gas negative pressure, external dust and iron chips cannot enter the clip, so as to prevent the offset from affecting the machining accuracy when the next workpiece is loaded.
(3) Advantages with traditional stand-alone equipment
The tempo of the production line is fast, the finishing time of the right end of the wheel bearing is about 15s, the refueling time of the joint robot to the main machine is 7s, and the production tempo of the whole line is 22s. The refueling time of 7s solves the artificial fatigue strength and refueling speed during the traditional manual refueling, because it is difficult to maintain high-intensity work in the 22s production line tempo. High stability, through high-quality purchased parts and high-rigid assembly quality, can ensure 24h uninterrupted operation of the equipment. High precision, right end of the hub bearing
1. Find out the cause of frequent equipment failures
The equipment has been deactivated for several years in the original use unit, and in the previous use, the spindle hydraulic locking mechanism, the spindle chuck, the jaw mechanism, the hydraulic circulation control system and the cutter holder operating positioning mechanism have all been compared. Big faults and maintenance. Therefore, the bottom gas of the device is insufficient, and there are a plurality of "nutrition" states. Due to the long-term use of the equipment, the hydraulic circulation system, mechanical transmission system, electrical detection and sensing system, servo motor drive system, hydraulic oil temperature circulation control system, hydraulic locking mechanism device and cutter holder cycle of the whole device are caused. There are different degrees of necrosis in the operation positioning system, etc., resulting in insensitivity of induction, system and mechanism operation is not smooth and not in place, in the large system of operation, control, detection and feedback of the whole equipment, in some small independent system units. There have been some dead spots, the detection component is slow to respond, and the component work has a fault point, resulting in endless equipment failures.
The equipment is not used for a long time. After the running mechanism of each system lacks the corresponding grinding machine, it is used as the reference positioning surface of the subsequent grinding process. Therefore, the height difference between the right end surface and the end surface of the raceway and the outer diameter of the end surface are strictly controlled. Its roundness. High-quality, machine tool application finite element method design, the torsional rigidity of the key parts of the bed, the saddle and the main shaft is greatly improved compared with the traditional machine, the thermal deformation is small, the spindle temperature rise is low, and the vibration is small. The automatic line of the finished finishing process after processing,
It makes up for the existing deficiencies of domestic equipment, solves the problem of slow processing of automatic processing of wheel hub bearings, accelerates the efficiency of automated production lines, and makes domestic existing equipment a step further into the international market. With the continuous development of wheel bearings, Its processing equipment is also constantly upgraded, and more automation equipment will be introduced to the market in the future.
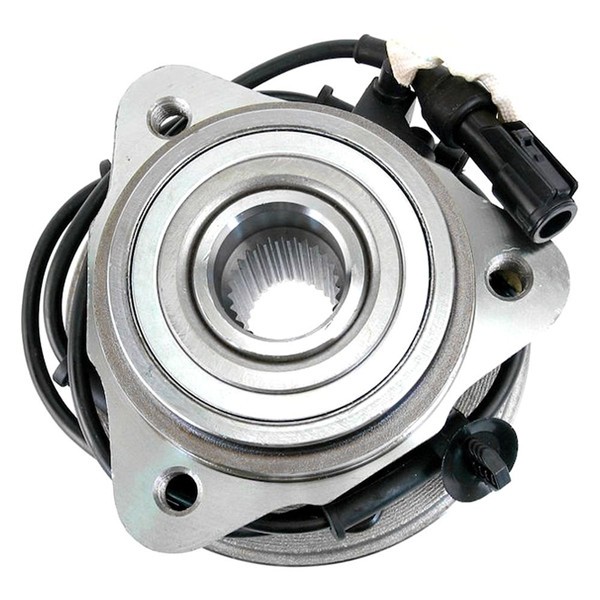
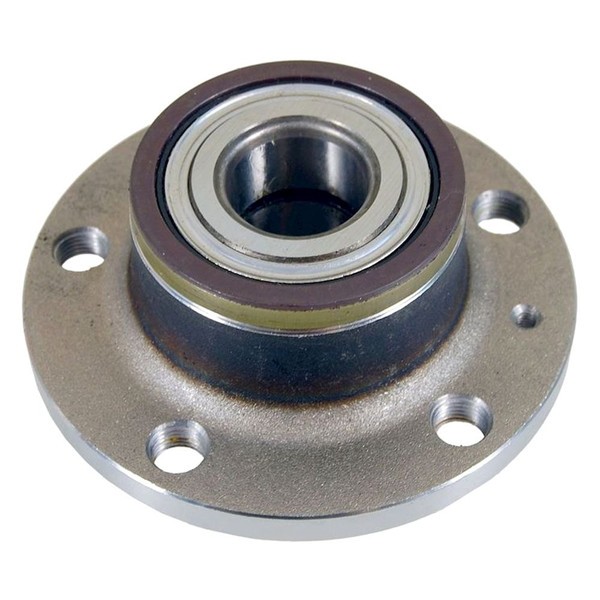
New Products
R900442260 SL10 PA2-4X Bosch Rexroth Check valve hydraulically pilot operated
R900517812 Z2FS 10-5-3X/V Germany Rexroth Throttle check valve
LS-G02-2CA-25-EN-645 Daikin LS Series Low Watt Type Solenoid Operated Valve
R900503335 DA20-1-5X/200-17 Rexroth Pressure cut-off valve, pilot-operated
R900560047 Z2S 22 B1-5X/SO60 Rexroth Check valves, pilot operated